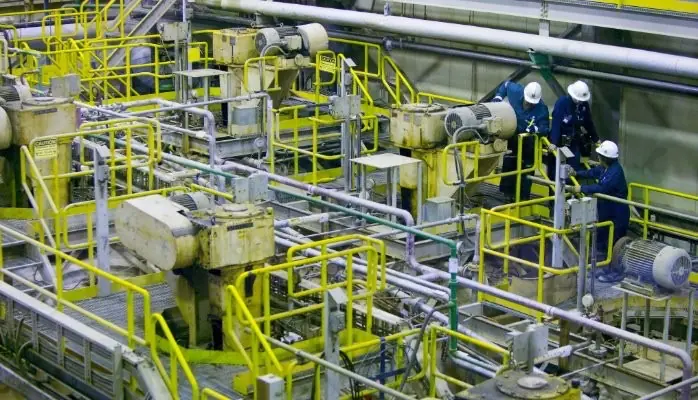
Project Cost and Sensitivity Analyses
Project cost and sensitivity analyses are critical tools in mining that help evaluate the financial feasibility and potential risks associated with mining operations. At our company, we specialize in conducting comprehensive analyses that provide insights into project economics, allowing clients to make informed decisions throughout the project lifecycle.
Our project cost analysis begins with a detailed assessment of all cost components, including capital expenditures (CapEx), operational expenditures (OpEx), and any additional expenses associated with regulatory compliance and environmental management. By meticulously estimating these costs, we create a clear financial framework that highlights the resources required for successful project execution.
Throughput Analyses
Throughput analyses are essential in the mining and mineral processing industries, focusing on the efficiency of material handling and processing operations. At our company, we specialize in conducting thorough throughput analyses that help identify bottlenecks and optimize production rates, ultimately enhancing overall operational performance.
Our approach begins with collecting and analyzing data on various stages of the mining process, including extraction, crushing, grinding, and separation. By assessing key metrics such as feed rates, recovery percentages, and cycle times, we can pinpoint areas where throughput may be compromised. This data-driven analysis enables us to develop targeted strategies for improving material flow and processing efficiency.
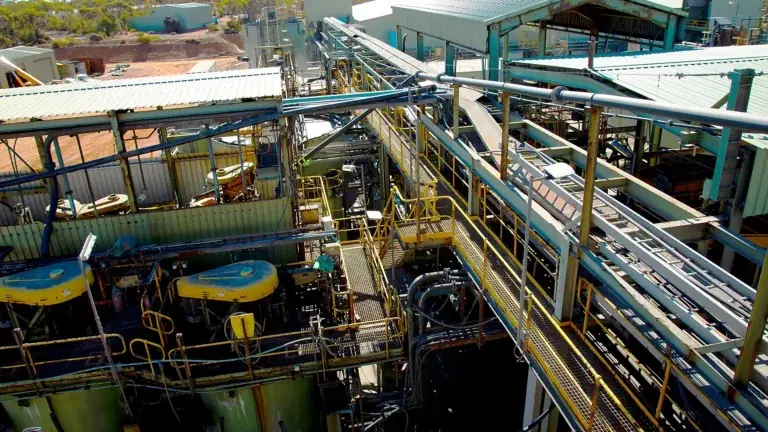
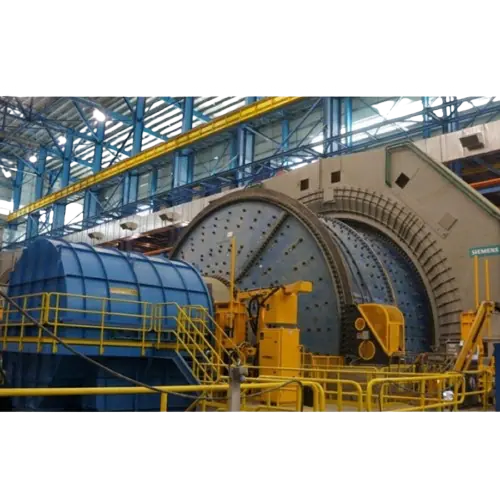
Comminution and Grinding Simulations and Modelling
Comminution and grinding simulations and modeling are vital components of mineral processing that play a significant role in optimizing the extraction of valuable minerals. At our company, we specialize in advanced simulation techniques that provide insights into the comminution process, enabling clients to enhance operational efficiency and improve recovery rates.
Our approach begins with the development of detailed models that represent the physical and chemical characteristics of the ore. We utilize sophisticated simulation software to analyze various grinding scenarios, allowing us to predict how different parameters—such as particle size distribution, mill speed, and media type—impact the grinding efficiency and overall performance. These models help us identify optimal operating conditions and inform equipment selection.
Flotation Optimization and Modelling
Flotation optimization and modelling are essential processes in mineral processing, focusing on improving the separation and recovery of valuable minerals from ore. At our company, we specialize in advanced flotation techniques and modelling approaches that enable clients to enhance their flotation operations, resulting in higher recovery rates and improved product quality.
Our optimization process begins with a thorough analysis of the ore’s mineralogical and chemical properties. By conducting detailed laboratory tests, we assess the flotation response of different minerals and identify the optimal reagents, pH levels, and flotation conditions required for effective separation. This foundational knowledge allows us to develop tailored flotation strategies that align with the specific characteristics of the ore being processed.
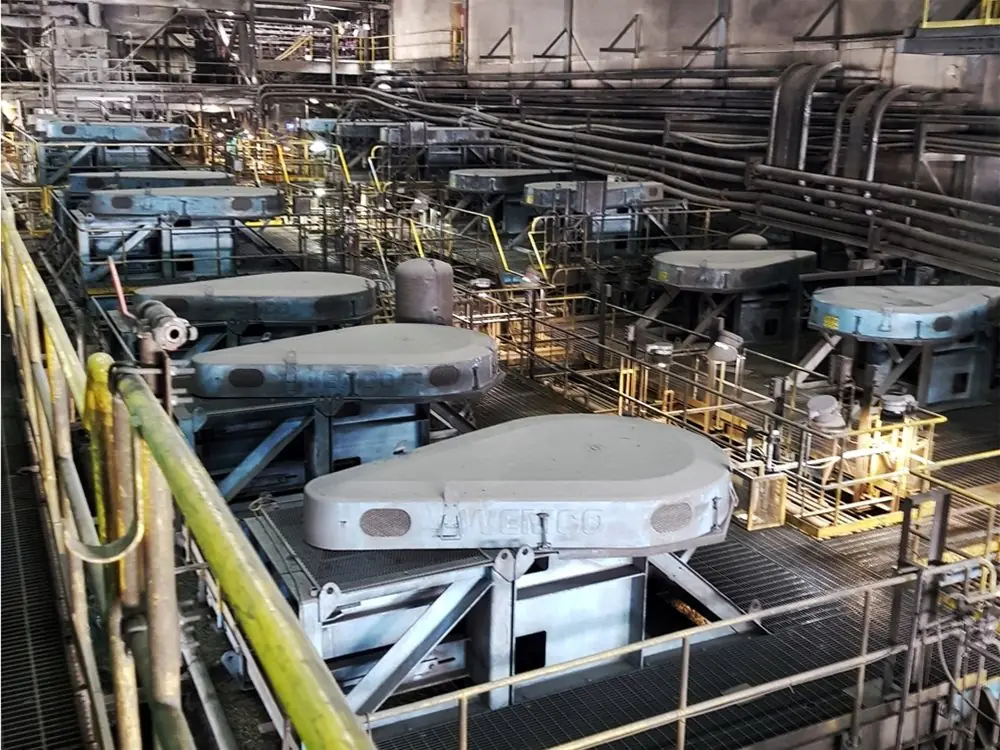
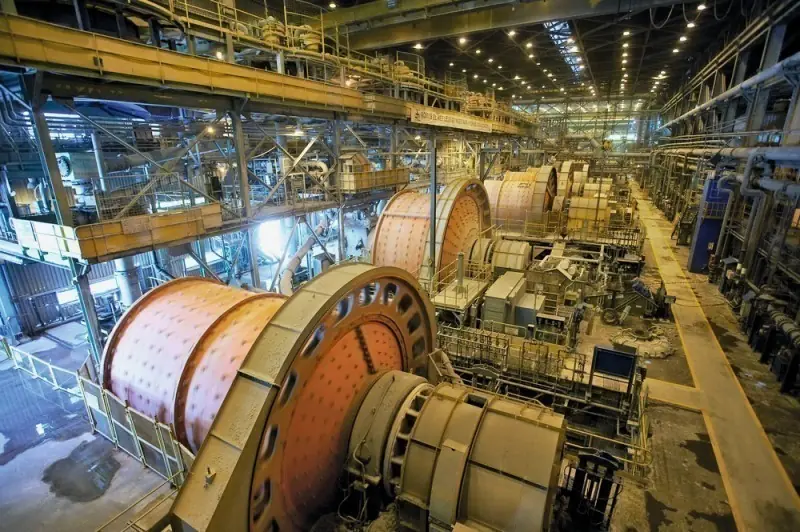
Block Diagrams
Block diagrams are essential tools used in various fields, including mining and mineral processing, to visually represent complex systems and processes. At our company, we leverage block diagrams to simplify the understanding of intricate workflows, helping clients grasp the relationships between different components of their operations.
Block diagrams provide a clear, visual representation of the overall system, illustrating the flow of materials, information, and energy throughout the mining process. Each block represents a specific unit operation—such as crushing, grinding, flotation, or tailings management—while arrows indicate the direction and flow of material or data between these operations. This clarity aids in identifying key processes, interdependencies, and potential bottlenecks in the workflow.
Process PFDs
Process Flow Diagrams (PFDs) are vital tools in the mining and mineral processing industries, providing a comprehensive visual representation of the flow of materials and processes within a system. At our company, we utilize PFDs to enhance clarity and communication regarding complex operations, helping clients optimize their workflows and improve operational efficiency.
A PFD outlines the key components of a process, including equipment, pipelines, and flow paths, allowing stakeholders to visualize how materials move through various stages of production. Each element in the diagram is clearly labeled, showcasing the relationship between different unit operations such as crushing, grinding, flotation, and tailings management. This clear depiction helps identify potential bottlenecks and areas for improvement in the process.
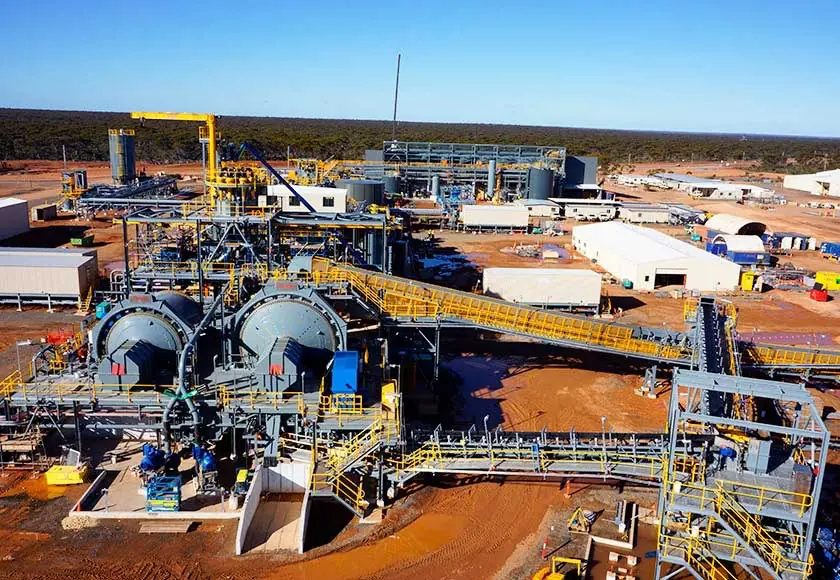
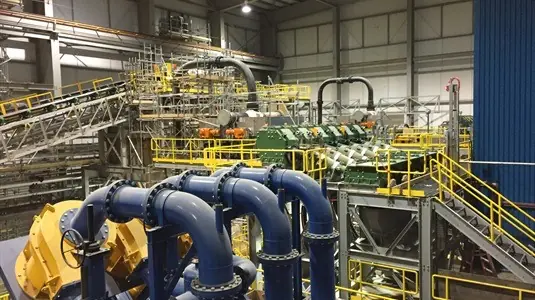
Process P&IDs
Piping and Instrumentation Diagrams (P&IDs) are critical documents in the mining and mineral processing industries, providing detailed representations of the piping, equipment, and control systems involved in a process. At our company, we utilize P&IDs to enhance operational clarity and facilitate effective communication among stakeholders, ensuring that all aspects of the process are well understood.
A P&ID illustrates the physical arrangement of equipment, piping, instrumentation, and control devices, clearly depicting how these elements interact within the system. Each component is represented with standardized symbols and notations, allowing for easy interpretation and communication of complex processes. This level of detail helps identify critical control points, safety measures, and potential areas for optimization.
Heat and Material Balances
Heat and material balances are essential analytical tools used in the mining and mineral processing industries to assess the flow of materials and energy throughout a process. At our company, we utilize these balances to optimize operations, enhance resource recovery, and ensure efficient energy use, ultimately driving the success of mining projects.
A heat balance evaluates the energy inputs and outputs in a system, identifying how energy is utilized and lost during various processes such as crushing, grinding, and flotation. By conducting a comprehensive heat balance, we can pinpoint areas where energy consumption can be reduced, leading to cost savings and improved sustainability. This analysis is critical for optimizing thermal processes, such as drying or smelting, where heat management is vital for operational efficiency.
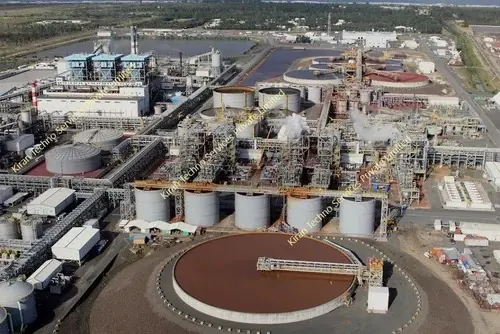
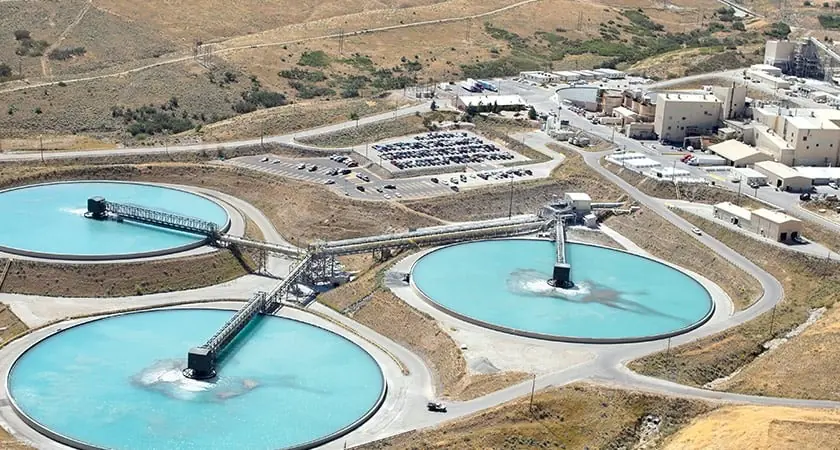
Water Balance
Our team utilizes advanced modeling techniques to develop accurate water balance models that reflect the unique characteristics of each mining operation. These models help to simulate different scenarios, enabling us to predict how changes in production levels, weather conditions, or operational practices may impact water usage. This proactive approach allows clients to develop effective water management strategies that align with their operational goals and regulatory requirements.
In addition to optimizing water usage, our water balance analyses help identify potential risks related to water scarcity or contamination. By understanding the dynamics of water flow within the mining operation, we can recommend measures to mitigate these risks and ensure compliance with environmental regulations.